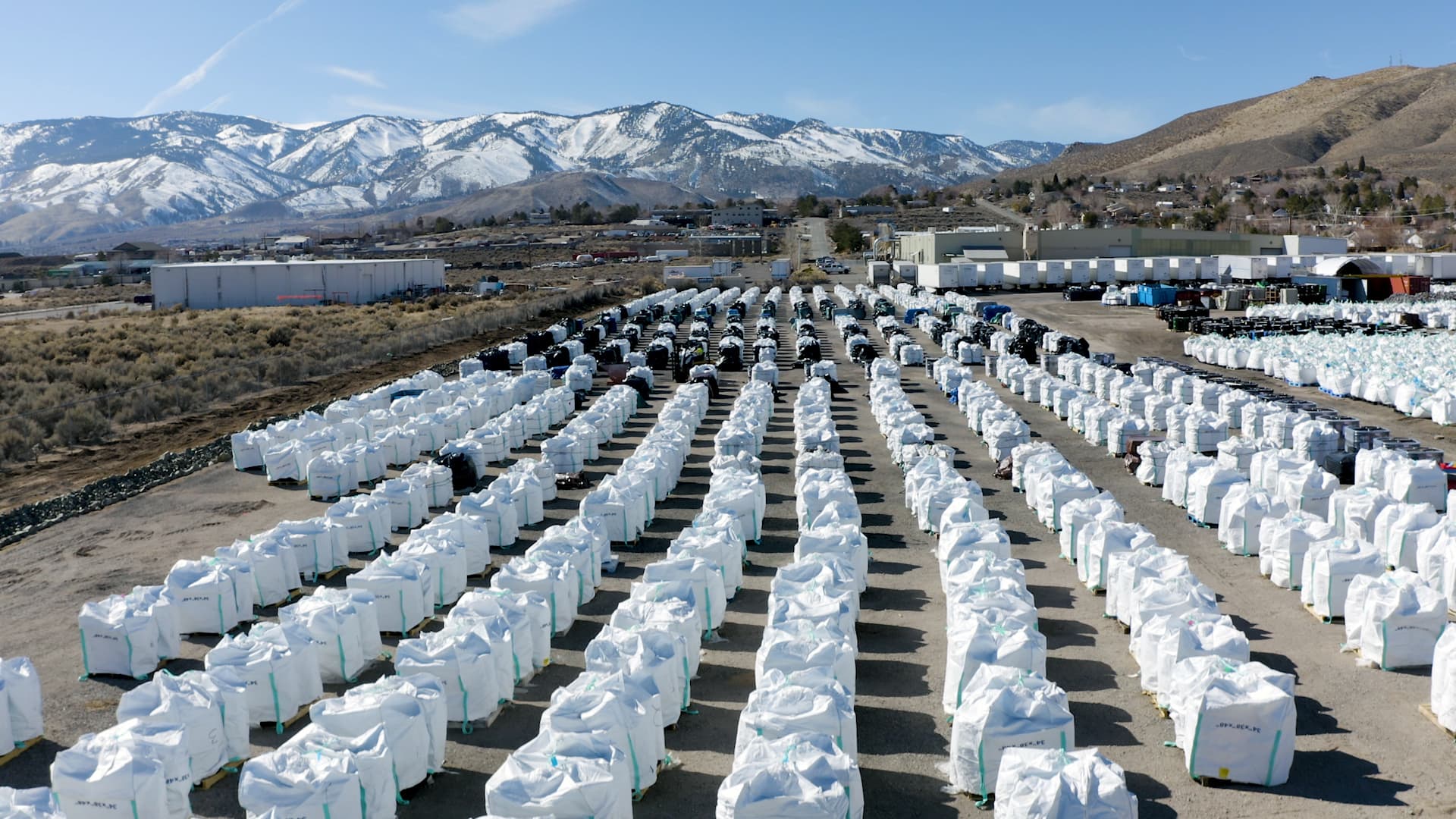
Recycling ‘end-of-life’ solar panels, wind turbines, is about to be climate tech’s big waste business
More Videos
Published
2 years agoon
By
adminSolarcycle CTO Pablo Dias and COO Rob Vinje show a solar panel laminate after it’s been cleanly separated from the glass to investors and partners. The laminate is where most of the value is contained in a panel, like silver, silicon, and copper.
Solarcycle
The growing importance of wind and solar energy to the U.S. power grid, and the rise of electric vehicles, are all key to the nation’s growing need to reduce dependence on fossil fuels, lower carbon emissions and mitigate climate change.
But at the same time, these burgeoning renewable energy industries will soon generate tons of waste as millions of photovoltaic (PV) solar panels, wind turbines and lithium-ion EV batteries reach the end of their respective lifecycles.
As the saying goes, though, one man’s trash is another man’s treasure. Anticipating the pileup of exhausted clean-energy components — and wanting to proactively avoid past sins committed by not responsibly cleaning up after decommissioned coal mines, oil wells and power plants — a number of innovative startups are striving to create a sustainable, and lucrative, circular economy to recover, recycle and reuse the core components of climate tech innovation.
Wind and solar energy combined to generate 13.6% of utility-scale electricity last year, according to the U.S. Energy Information Administration (EIA), and those numbers will undoubtedly rise as renewable energy continues to scale up. Some leading utilities across the nation are far ahead of that pace already.
Meanwhile, sales of all-electric vehicles rose to 5.8% of the total 13.8 million vehicles Americans purchased in 2022, up from 3.2% in 2021. And with the Environmental Protection Agency’s newly proposed tailpipe emissions limits and power plant rules, EV sales could capture a 67% market share by 2032 and more utilities be forced to accelerate their power generation transition.
Solarcycle is a prime example of the companies looking to solve this climate tech waste problem of the future. Launched last year in Oakland, California, it has since constructed a recycling facility in Odessa, Texas, where it extracts 95% of the materials from end-of-life solar panels and reintroduces them into the supply chain. It sells recovered silver and copper on commodity markets and glass, silicon and aluminum to panel manufacturers and solar farm operators.
“Solar is becoming the dominant form of power generation,” Solarcycle CEO Suvi Sharma said, citing an EIA report stating that 54% of new utility-scale electric-generating capacity in the U.S. this year will come from solar. “But with that comes a new set of challenges and opportunities. We have done a phenomenal job making solar efficient and cost-effective, but really have not done anything yet on making it circular and dealing with the end-of-life [panels].”
Keeping solar panels out of landfills
The average lifespan of a solar panel is about 25 to 30 years, and there are more than 500 million already installed across the country, Sharma said, ranging from a dozen on a residential home’s rooftop to thousands in a commercial solar farm. With solar capacity now rising an average of 21% annually, tens of millions more panels will be going up — and coming down. Between 2030 and 2060, roughly 9.8 million metric tons of solar panel waste are expected to accumulate, according to a 2019 study published in Renewable Energy.
Currently, about 90% of end-of-life or defective solar panels end up in landfills, largely because it costs far less to dump them than to recycle them. “We see that gap closing over the next five to 10 years significantly,” Sharma said, “through a combination of recycling becoming more cost-effective and landfilling costs only increasing.”

Indeed, the market for recycled solar panel materials is expected to grow exponentially over the next several years. A report by research firm Rystad Energy stated they’ll be worth more than $2.7 billion in 2030, up from only $170 million last year, and accelerate to around $80 billion by 2050. The Department of Energy’s National Renewable Laboratory (NREL) found that with modest government support, recycled materials can meet 30%-50% of solar manufacturing needs in the U.S. by 2040.
Both the Bipartisan Infrastructure Law and the Inflation Reduction Act (IRA) provide tax credits and funding for domestic manufacturing of solar panels and components, as well as research into new solar technologies. Those provisions are intended to cut into China’s dominant position in the global solar panel supply chain, which exceeds 80% today, according to a recent report from the International Energy Agency.
One recipient of this federal funding is First Solar, the largest solar panel manufacturer in the U.S. Founded in 1999 in Tempe, Arizona, the company has production facilities in Ohio and another under construction in Alabama. It has been awarded $7.3 million in research funds to develop a new residential rooftop panel that is more efficient than current silicon or thin-film modules.
First Solar has maintained an in-house recycling program since 2005, according to an email from chief product officer Pat Buehler. “We recognized that integrating circularity into our operations was necessary to scale the business in a sustainable way,” he wrote. But rather than extracting metals and glass from retired panels and manufacturing scrap, “our recycling process provides closed-loop semiconductor recovery for use in new modules,” he added.
Massive wind turbines, blades are almost all recyclable
Retired wind turbines present another recycling challenge, as well as business opportunities. The U.S. wind energy industry started erecting turbines in the early 1980s and has been steadily growing since. The American Clean Power Association estimates that today there are nearly 72,000 utility-scale turbines installed nationwide — all but seven of them land-based — generating 10.2% of the country’s electricity.
Although the industry stalled over the past two years, due to supply chain snags, inflation and rising costs, turbine manufacturers and wind farm developers are optimistic that the tide has turned, especially given the subsidies and tax credits for green energy projects in the IRA and the Biden administration’s pledge to jumpstart the nascent offshore wind sector.
The lifespan of a wind turbine is around 20 years, and most decommissioned ones have joined retired solar panels in landfills. However, practically everything comprising a turbine is recyclable, from the steel tower to the composite blades, typically 170 feet long, though the latest models exceed 350 feet.
Between 3,000 and 9,000 blades will be retired each year for the next five years in the U.S., and then the number will increase to between 10,000 and 20,000 until 2040, according to a 2021 study by NREL. By 2050, 235,000 blades will be decommissioned, translating to a cumulative mass of 2.2 million metric tons — or more than 60,627 fully loaded tractor trailers.
How the circular renewable energy economy works
Players in the circular economy are determined not to let all that waste go to waste.
Knoxville-based Carbon Rivers, founded in 2019, has developed technology to shred not only turbine blades but also discarded composite materials from the automotive, construction and marine industries and convert them through a pyrolysis process into reclaimed glass fiber. “It can be used for next-generation manufacturing of turbine blades, marine vessels, composite concrete and auto parts,” said chief strategy officer David Morgan, adding that the process also harvests renewable oil and synthetic gas for reuse.
While processing the shredded materials is fairly straightforward, transporting massive turbine blades and other composites over long distances by rail and truck is more complicated. “Logistics is far and away the most expensive part of this entire process,” Morgan said.
In addition to existing facilities in Tennessee and Texas, Carbon Rivers plans to build sites in Florida, Pennsylvania and Idaho over the next three years, strategically located near wind farms and other feedstock sources. “We want to build another five facilities in the U.K. and Europe, then get to the South American and Asian markets next,” he said.
In the spirit of corporate sustainability — specifically not wanting their blades piling up in landfills — wind turbine manufacturers themselves are contracting with recycling partners. In December 2020, General Electric’s Renewable Energy unit signed a multi-year agreement with Boston-based Veolia North America to recycle decommissioned blades from land-based GE turbines in the U.S.
Veolia North America opened up a recycling plant in Missouri in 2020, where it has processed about 2,600 blades to date, according to Julie Angulo, senior vice president, technical and performance. “We are seeing the first wave of blades that are 10 to 12 years old, but we know that number is going to go up year-on-year,” she said.
Using a process known as kiln co-processing, Veolia reconstitutes shredded blades and other composite materials into a fuel it then sells to cement manufacturers as a replacement for coal, sand and clay. The process reduces carbon dioxide emissions by 27% and consumption of water by 13% in cement production.
“Cement manufacturers want to walk away from coal for carbon emissions reasons,” Angulo said. “This is a good substitute, so they’re good partners for us.”
GE’s wind turbine competitors are devising ways to make the next generation of blades inherently more recyclable. Siemens Gamesa Renewable Energy has begun producing fully recyclable blades for both its land-based and offshore wind turbines and has said it plans to make all of its turbines fully recyclable by 2040. Vestas Wind Systems has committed to producing zero-waste wind turbines by 2040, though it has not yet introduced such a version. In February, Vestas introduced a new solution that renders epoxy-based turbine blades to be broken down and recycled.
Electric vehicle lithium-ion battery scrap
Lithium-ion batteries have been in use since the early 1990s, at first powering laptops, cell phones and other consumer electronics, and for the past couple of decades EVs and energy storage systems. Recycling of their valuable innards — lithium, cobalt, nickel, copper — is focused on EVs, especially as automakers ramp up production, including building battery gigafactories. But today’s EV batteries have a lifespan of 10-20 years, or 100,000-200,000 miles, so for the time being, recyclers are primarily processing battery manufacturers’ scrap.
Toronto-based Li-Cycle, launched in 2016, has developed a two-step technology that breaks down batteries and scrap to inert materials and then shreds them, using a hydrometallurgy process, to produce minerals that are sold back into the general manufacturing supply chain. To avoid high transportation costs for shipping feedstock from various sites, Li-Cycle has geographically interspersed four facilities — in Alabama, Arizona, New York and Ontario — where it’s deconstructed. It is building a massive facility in Rochester, New York, where the materials will be processed.
“We’re on track to start commissioning the Rochester [facility] at the end of this year,” said Li-Cycle’s co-founder and CEO Ajay Kochhlar. Construction has been funded by a $375 loan from the Department of Energy (DOE), he said, adding that since the company went public, it’s also raised about $1 billion in private deals.
A different approach to battery recycling is underway at Redwood Materials, founded outside of Reno, Nevada, in 2017 by JB Straubel, the former chief technology officer and co-founder of Tesla. Redwood also uses hydrometallurgy to break down batteries and scrap, but produces anode copper foil and cathode-active materials for making new EV batteries. Because the feedstock is not yet plentiful enough, the nickel and lithium in its cathode products will only be about 30% from recycled sources, with the remainder coming from newly mined metals.

“We’re aiming to produce 100 GWh/year of cathode-active materials and anode foil for one million EVs by 2025,” Redwood said in an email statement. “By 2030, our goal is to scale to 500 GWh/year of materials, which would enable enough batteries to power five million EVs.”
Besides its Nevada facility, Redwood has broken ground on a second one in Charleston, South Carolina. The privately held company said it has raised more than $1 billion, and in February it received a conditional commitment from the DOE for a $2-billion loan from the DOE as part of the IRA. Last year Redwood struck a multi-billion dollar deal with Tesla’s battery supplier Panasonic, and it’s also inked partnerships with Volkswagen Group of America, Toyota, Ford and Volvo.
Ascend Elements, headquartered in Westborough, Massachusetts, utilizes hydrometallurgy technology to extract cathode-active material mostly from battery manufacturing scrap, but also spent lithium-ion batteries. Its processing facility is strategically located in Covington, Georgia, a state that has attracted EV battery makers, including SK Group in nearby Commerce, as well as EV maker Rivian, near Rutledge, and Hyundai, which is building an EV factory outside of Savannah.
Last October, Ascend began construction on a second recycling facility, in Hopkinsville, Kentucky, using federal dollars earmarked for green energy projects. “We have received two grant awards from the [DOE] under the Bipartisan Infrastructure Law that totaled around $480 million,” said CEO Mike O’Kronley. Such federal investments, he said, “incentivizes infrastructure that needs to be built in the U.S., because around 96% of all cathode materials are made in East Asia, in particular China.”
As the nation continues to build out a multi-billion-dollar renewable energy supply chain around solar, wind and EVs, simultaneously establishing a circular economy to recover, recycle and reuse end-of-life components from those industries is essential in the overarching goal of battling climate change.
“It’s important to make sure we keep in mind the context of these emerging technologies and understand their full lifecycle,” said Garvin Heath, a senior energy sustainability analyst at NREL. “The circular economy provides a lot of opportunities to these industries to be as sustainable and environmentally friendly as possible at a relatively early phase of their growth.”
You may like
Environment
Heybike Hauler cargo e-bike hits $999 low ($500 off), EcoFlow DELTA Pro with transfer switch at $1,709 low + other units, Worx, more
Published
1 hour agoon
July 7, 2025By
admin

It’s the calm before the storm as everyone prepares for Amazon’s Prime Day Sale event starting tomorrow morning (July 8), but that doesn’t mean there aren’t still solid Green Deals coming in today. Leading the pack is Heybike’s Hauler Cargo e-bike that is back down at its $999 low for the second time. Right behind it is EcoFlow’s final early Prime Day flash sale on three units, with the DELTA Pro Portable Power Station bundle coming back around at a $1,709 low that also gives you a free transfer switch and RAPID 5,000mAh power bank, as well as savings on DELTA 3 and WAVE 3 bundles from $529. We also have Worx’s Nitro 20V 8-inch Cordless Pole Chainsaw at its best 2025 rate of $119, as well as EGO’s 56V 21-inch Cordless Electric Lawn Mower with a 5.0Ah battery and rapid charger at $365. Plus, there’s all the hangover Green Deals still seeing savings in our one-stop-shop July 4th hub in the links at the bottom of the page – with many of the savings ending tonight!
Head below for other New Green Deals we’ve found today and, of course, Electrek’s best EV buying and leasing deals. Also, check out the new Electrek Tesla Shop for the best deals on Tesla accessories.
Affordably carry cargo with Heybike’s single or dual-battery Hauler e-bike starting from a $999 low
As part of its Prime Day e-bike Sale, Heybike is offering its Hauler Cargo Single-Battery e-bike at $999 shipped, while the dual-battery counterpart is down at $1,399 shipped. You’d normally shell out $1,499 and $1,899 for these two setups at full price, though discounts regularly bring things down to $1,199 and $1,599, which we have seen go lower a few select times in 2025. Only once before have we seen these two low prices appear, back during the brand’s Memorial Day Sale, with you getting another chance at the $500 savings here today.
Heybike’s Hauler e-bike comes as an affordable means to transport precious cargo, with the 750W brushless geared hub motor peaking at up to 1,400W to tackle inclines and for better pick-up when you’ve got packages, groceries, and more on board. It can max out at 28 MPH speeds in states where it’s allowed, and comes with the two battery options that largely depend on how much travel time you need, with the solo-battery setup giving you up to 55 miles of pedal assisted support and the dual-battery setup increasing that travel range up to 85 miles.
Advertisement – scroll for more content
The Heybike Hauler e-bike boasts a 440-pound payload, as well as foldable running boards for when you want to bring a passenger along, not to mention the obvious integrated rear cargo rack that doubles as the seat. For the price right now, you’re also getting a solid lineup of features, including hydraulic front suspension, hydraulic disc brakes, puncture-protected tires, a Shimano 7-speed derailleur, an auto-on LED headlight, a brake-lighting integrated taillight, and an LCD screen for data and setting adjustments.
You can check out Heybike’s full lineup of Prime Day e-bike deals on the landing page here.
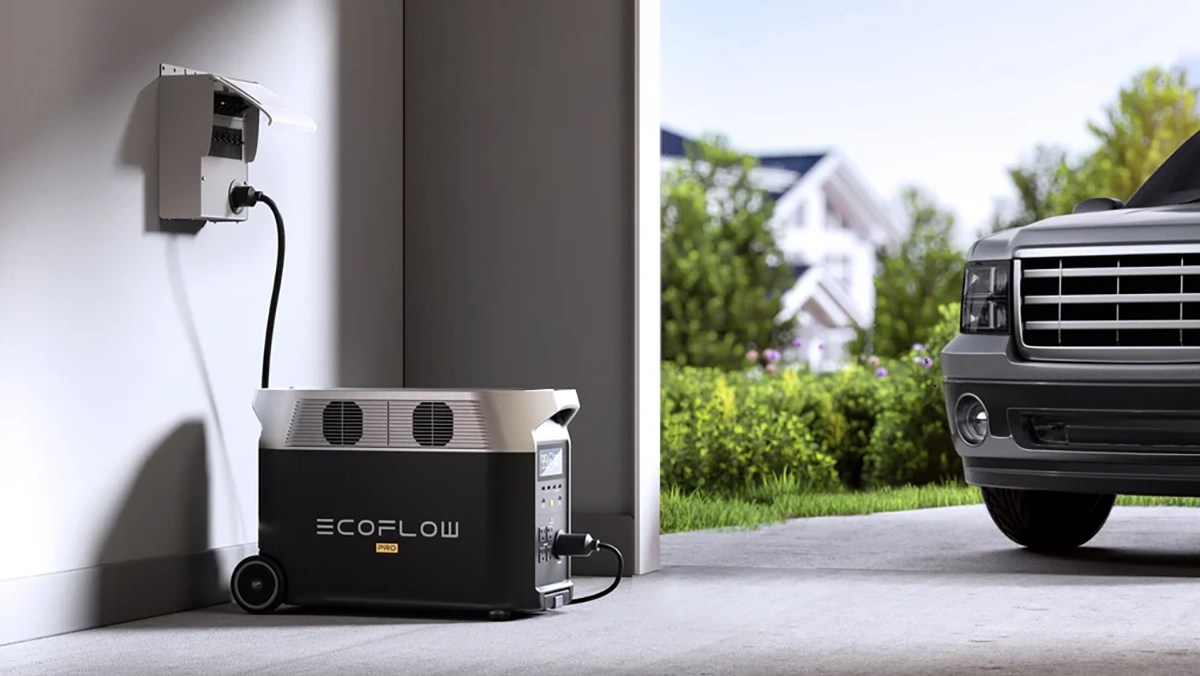
Get sectional backup support with EcoFlow’s DELTA Pro and transfer switch + free power bank at $1,709 low
It’s the final day of EcoFlow’s early Prime Day Sale, and the brand’s final flash sale is in full swing through the rest of the day. The flash savings here are taking up to 54% off three units – two power station bundles and a bundle for the brand’s newest AC/heater solution. Leading the sale is the DELTA Pro Portable Power Station that comes with a free transfer switch for $1,709.05 shipped, after using the code EFPDAFF5 at checkout for an additional 5% savings – plus, you’ll also be getting a free RAPID 5,000mAh power bank thrown in too. We’ve been seeing many different flash sales focusing on the DELTA Pro at this same rate during this sale, which usually carries a $3,699 MSRP, though it is regularly sitting around $1,999 from Amazon (currently $1,784 there). Not only are you getting another chance at the biggest savings and the best price here, but you’re doing so while also getting the means for sectional home backup support.
One of the best and most expansive of EcoFlow’s legacy models, the DELTA Pro power station is ready to cover your campsites, outdoor gatherings, and home backup emergencies with a 3,600Wh LiFePO4 capacity that you can expand as high as 25kWh with future investments. There are 14 port options here, through which the station provides up to a steady 3,600W output that can surge up to 7,200W to cover larger appliances. It comes with three primary means to recharge: plugged into a standard outlet, through your car’s auxiliary port, or by connecting up to a maximum 1,600W solar input. The included transfer switch gives you sectional backup support of up to six circuits in your home or on an RV, with it pre-wired for easier installation.
You can also pick up the brand’s DELTA 3 Portable Power Station with a free protective bag at $529 shipped, down from its usual $778 pricing. This is a smaller and more affordable backup option that has a 1,024Wh LiFePo4 capacity and can be expanded up to 5,120Wh with various expansion batteries from across the DELTA ecosystem. It provides 1,800W output, surging to 2,200W when needed, and has 13 total output ports to use for connections to devices and appliances. It also boasts an expanded list of recharging options, including through an AC outlet, with a max 500W solar input, through car charging, generator charging, or there’s the multi-charging option of AC and solar together.
The last of these offers gives you the latest WAVE 3 Portable AC and Heater with an add-on battery and a free bag at $899 shipped, coming down from $1,299. With the battery included here, you can get up to 8 hours of wireless cooling/heating in your tent, car, or anywhere else you’re settling down. The 1,800W output here can “drop temperatures by 15 degrees in 15 minutes,” while the 2,000W heating output hits similar speeds, “raising the temperature by 17 degrees in 15 minutes” – with it able to cover 120 to 180 square feet spaces. There’s even some cool smart control expansions here, including the PetCare mode that automatically starts cooling once temperatures reach 77 degrees, among others.
Be sure to check out EcoFlow’s full early Prime Day Sale lineup here before it ends later tonight.

Get 13.3 feet of reach with Worx’s telescoping Nitro 20V 8-inch cordless pole chainsaw at $119 annual low
Amazon is offering the best pricing of the last year on the Worx Nitro 20V 8-inch Cordless Pole Chainsaw at $119 shipped. Normally, you’d have to shell out $170 for this tool at full price, which we’ve seen discounts taking as low as $120 once over the last 12 months, with prices otherwise keeping above $129. While it has gone lower in past years, you’re looking at the best price we have tracked since summer 2024, giving you $51 in savings off its going rate.
You’ll have plenty of reach to trim high branches with this Worx Nitro pole chainsaw, especially with the telescoping pole allowing for tool-free extensions up to 13.3 feet – plus, it weighs in at just 8 pounds, making it easy to manage and operate, despite varying operator sizes. The 8-inch bar and chain has three different cutting angles (0 degrees, 15 degrees, and 30 degrees) it can be set to, with the automatic oiler keeping things lubricated and running smoothly as you work. What’s more, your comfort has been taken into account with the 180-degree rotating rear handle, allowing you to easily switch between vertical and horizontal cutting positions.

Bring home EGO’s 56V 21-inch cordless electric mower with a 5.0Ah battery and rapid charger at $365
Amazon is offering the EGO Power+ 56V 21-inch Cordless Electric Lawn Mower with 5.0Ah battery and rapid charger at $364.60 shipped. This package would normally go for $430 at full price, which we’ve mostly seen it keeping at over the last 12 months, with few large price cuts on the books in that timeframe. While we have seen it go as low as $309 in the past, over the last 12 months, the rate we’re seeing today has only been beaten out by a short-lived drop to $350 back in April, with it otherwise being the best price we’ve spotted this year thanks to the $65 markdown.
You’ll get a much more budget-friendly means to tackle lawn care with this 56V 21-inch model over EGO’s higher-end mowers, giving you the torque of a gas engine without the noise and fumes. With the included 5.0Ah battery, the brushless motor will get up to 45 continuous minutes of runtime, while the rapid charger can have it back to full at much faster rates than a standard charger. There are six cutting height levels to adjust between (from 1.5 to 4 inches), as well as the versatility to side discharge, mulch, or collect clippings into the two-bushel bag. Not only does it come with an IPX4 weather-resistance construction, but it starts up at the push of a button and folds to a more compact size for easier storage options.
Best Summer EV deals!
- Ford Bronco e-bike (use code PDSG5OFF): $4,000 (Reg. $4,500)
- Ford Mustang e-bike (use code PDSG5OFF): $3,500 (Reg. $4,000)
- Aventon Ramblas Electric Mountain Bike: $2,599 (Reg. $2,899)
- Heybike Hero Carbon Fiber All-Terrain 750W mid-drive e-bike: $2,599 (Reg. $3,099)
- Ride1Up Prodigy v2 Brose Mid-Drive Gates Belt CVT e-bike: $2,595 (Reg. $2,795)
- Velotric Nomad 2X Multi-Terrain Camo e-bike with $50 bundle: $2,499 (No price cut)
- Ride1Up Revv 1 DRT Off-Road Moped-Style e-bike: $2,495 (Reg. $2,595)
- Ride1Up Revv 1 Full Suspension Moped-Style e-bike: $2,395 (Reg. $2,595)
- Heybike Hero Carbon Fiber All-Terrain 1,000W rear-hub e-bike: $2,299 (Reg. $2,599)
- Ride1Up Prodigy v2 Brose Mid-Drive 9-Speed e-bike: $2,095 (Reg. $2,495)
- Velotric Nomad 2 All-Terrain e-bike with $120 bundle (new model): $1,999 (No price cut)
- Rad Power Radster Road Commuter e-bike: $1,999 (Reg. $2,199)
- Rad Power Radster Trail Off-Road e-bike: $1,999 (Reg. $2,199)
- Lectric XPedition 2.0 35Ah Cargo e-bike w/ up to $703 bundle: $1,999 (Reg. $2,702)
- Tenways AGO X All-Terrain e-bike with $307 bundle: $1,899 (Reg. $2,499)
- Velotric Breeze 1 Cruiser e-bike with $150 bundle (new model): $1,799 (No price cut)
- Aventon Pace 4 Smart Cruiser e-bike (new model, first discount): $1,699 (Reg. $1,799)
- Lectric XPedition 2.0 26Ah Cargo e-bike w/ $554 bundle: $1,699 (Reg. $2,253)
- Lectric XPeak 2.0 Long-Range Off-Road e-bike with $316 bundle: $1,699 (Reg. $1,915)
- Aventon Abound Cargo e-bike: $1,599 (Reg. $1,999)
- Aventon Aventure 2 All-Terrain e-bike (2025 low): $1,599 (Reg. $1,999)
- Lectric XPeak 2.0 Standard Off-Road e-bike with $227 bundle: $1,499 (Reg. $1,726)
- Tenways CGO600 Pro e-bikes with $118 bundle: $1,499 (Reg. $1,899)
- Velotric Nomad 1 Plus All-Terrain e-bike with $69 bundle : $1,399 (Reg. $1,899)
- Fold 1 Plus e-bike with $120 bundle (new model): $1,499 (No price cut)
- Lectric XP Trike with $405 bundle: $1,499 (Reg. $1,904)
- Lectric XPedition 2.0 13Ah Cargo e-bike with $326 bundle: $1,399 (Reg. $1,725)
- Aventon Level 2 Commuter e-bike (2025 low): $1,399 (Reg. $1,899)
- Ride1Up Roadster V3 Lightweight Premium e-bike: $1,395 (Reg. $1,495)
- Velotric T1 ST Plus e-bike with $82 bundle (2025 low): $1,299 (Reg. $1,649)
- Lectric XPress 750 Commuter e-bikes with $336 bundle: $1,299 (Reg. $1,635)
- Lectric XP4 750 LR Folding Utility e-bikes with $356 bundle: $1,299 (Reg. $1,655)
- Heybike Brawn Off-Road e-bike: $1,299 (Reg. $1,799)
- Velotric Discover 1 Plus Commuter e-bike with $83 bundle (2025 low): $1,199 (Reg. $1,699)
- Lectric XP Lite 2.0 JW Black LR e-bike with $414 bundle: $1,099 (Reg. $1,513)
- Ride1Up Portola Folding e-bike with BOGO accessory promo: $995 (Reg. $1,095)
- Lectric XP4 Standard Folding Utility e-bikes with $79 bundle: $999 (Reg. $1,078)
- Lectric XP 3.0 Long-Range e-bikes (clearance price cut): $999 (Reg. $1,199)
- Lectric XP Lite 2.0 Long-Range e-bikes with up to $414 bundles: $999 (Reg. $1,413)
- Heybike Hauler Single-Battery Cargo e-bike: $999 (Reg. $1,499)
- Rad Power RadExpand 5 Folding e-bike (new low): $999 (Reg. $1,599)
- Navee ST3 Pro Electric Scooter (new model): $760 (Reg. $1,014)
- Fold 1 Lite e-bike (new all-time low): $599 (Reg. $1,099)
- Navee GT3 Pro Electric Scooter (new model): $520 (Reg. $714)

Best new Green Deals landing this week
The savings this week are also continuing to a collection of other markdowns. To the same tune as the offers above, these all help you take a more energy-conscious approach to your routine. Winter means you can lock in even better off-season price cuts on electric tools for the lawn while saving on EVs and tons of other gear.
FTC: We use income earning auto affiliate links. More.
Environment
Arizona brings a huge grid battery online ahead of peak demand
Published
2 hours agoon
July 7, 2025By
admin

One of Arizona’s biggest grid battery storage projects is now online and helping power homes as the summer heat ramps up.
Recurrent Energy, a subsidiary of Canadian Solar, just brought its 1,200 MWh Papago Storage facility in Maricopa County into commercial operation. The big grid battery is now supplying stored electricity to Arizona Public Service (APS), the state’s largest utility, in time for peak air-conditioning season.
Papago is the first of three Recurrent projects with APS. Together, they’ll provide 1,800 MWh of storage and 150 MW of solar power. That’s enough to run about 72,000 homes for four hours and provide year-round solar for another 24,000 homes.
“Summer is here, and we’re ready to serve APS customers with the energy they need when they need it,” said APS director of resource acquisition Derek Seaman.
Advertisement – scroll for more content
The Arizona Corporation Commission chair, Kevin Thompson, noted that bringing online one of Arizona’s largest battery storage projects during a critical time when energy demand is skyrocketing is a milestone.
Canadian Solar’s e-STORAGE arm built the project and will keep it running under a long-term agreement.
Recurrent CEO Ismael Guerrero said, “We’re proud to deliver flexible capacity that meets the state’s growing energy needs and grateful for APS’s continued partnership.”

If you live in an area that has frequent natural disaster events, and are interested in making your home more resilient to power outages, consider going solar and adding a battery storage system. To make sure you find a trusted, reliable solar installer near you that offers competitive pricing, check out EnergySage, a free service that makes it easy for you to go solar. They have hundreds of pre-vetted solar installers competing for your business, ensuring you get high quality solutions and save 20-30% compared to going it alone. Plus, it’s free to use and you won’t get sales calls until you select an installer and share your phone number with them.
Your personalized solar quotes are easy to compare online and you’ll get access to unbiased Energy Advisers to help you every step of the way. Get started here. –trusted affiliate link*
FTC: We use income earning auto affiliate links. More.
Environment
The Porsche Cayenne EV flexes its power towing 3-tons in public
Published
2 hours agoon
July 7, 2025By
admin

Porsche promises the new electric SUV will “set new standards,” and it’s already proving it. Ahead of its upcoming launch, the Porsche Cayenne EV proved its might by towing a 100-year-old classic car and trailer weighing around 3 tons in public.
Porsche Cayenne EV flexes its performance in public
The Porsche Cayenne EV is already smashing records, and it’s not even out yet. Last month, a prototype beat every gas-powered SUV, setting a new SUV record at the Shelsley Walsh hill climb by more than four seconds.
Now, it’s at it again. Porsche showcased a near-production-ready Cayenne EV prototype in England for the first time as part of a public film shoot.
The camouflaged Cayenne EV showcased its impressive power by towing a 100-year-old classic car weighing over 2 tons. Including the trailer, the total weight was around 3 tons.
Advertisement – scroll for more content
British TV presenter Richard Hammond took the Cayenne EV from his workshop in Hereford to his garage, towing the classic car behind.
According to Hammond, the electric SUV “handled it effortlessly,” adding, “We were trailing significant weight behind us, but you wouldn’t know it.”

Porsche designed the Cayenne EV and its high-voltage system, “to be one of the first BEVs in the world to achieve a towing capacity of up to 3.5 tonnes.” Depending on the configuration, it will be just as capable, if not more, than the current combustion-engine Cayenne.
As Michael Schätzle, Vice President of the Product Line Cayenne, explained, “That’s why we didn’t want to make any compromises in the development of the all-electric model.”

The Porsche Cayenne EV was initially set to launch this year, but it’s now expected to debut in production form later this year as a 2026 model. A “conspicuously camouflaged prototype” will be on display at the Goodwood Festival of Speed from July 10 to July 13.
More information, including prices and specifications, will be revealed closer to launch. However, we do know that it will be based on the PPE platform, the same one underpinning the Macan EV and the Audi Q6 e-Tron.
The Macan EV has an EPA-estimated range of 308 miles. On the European WLTP scale, it’s rated at 613 km (381 miles). However, Porsche said the platform will receive “comprehensive upgrades” for the Cayenne.
FTC: We use income earning auto affiliate links. More.
Trending
-
Sports3 years ago
‘Storybook stuff’: Inside the night Bryce Harper sent the Phillies to the World Series
-
Sports1 year ago
Story injured on diving stop, exits Red Sox game
-
Sports2 years ago
Game 1 of WS least-watched in recorded history
-
Sports2 years ago
MLB Rank 2023: Ranking baseball’s top 100 players
-
Sports4 years ago
Team Europe easily wins 4th straight Laver Cup
-
Environment2 years ago
Japan and South Korea have a lot at stake in a free and open South China Sea
-
Sports2 years ago
Button battles heat exhaustion in NASCAR debut
-
Environment2 years ago
Game-changing Lectric XPedition launched as affordable electric cargo bike