Flow Batteries Are An Area Of Strong Innovation & Opportunity
More Videos
Published
3 years agoon
By
adminAs part of my ongoing deep dives into different portions of the climate solution space, I’ve been working my way through grid energy storage solutions. That led to my recent pair of broad articles on grid storage, Grid Storage Winners Part 1: Assessing The Major Technologies, and Grid Storage Winners Part 2: How Much Of Which Storage By When? The multi-factorial assessment found that lithium-ion batteries will have a smaller role than many assume, that closed-loop pumped hydro storage (a subject I’ve published on many times) would be a very large part of the solution, and that redox flow batteries would be second only to pumped hydro in global application.
As a teaser, Agora Energy Technologies’ CO2-based redox flow battery technology has won the 2021 Hello Tomorrow global deeptech competition across 5,000 entrants from 128 countries, the just announced 2021 Keeling Curve Prize and the CEO has been made a 2021 Cartier Women’s Initiative Fellow in science and technology. More on Agora in subsequent articles.
This ARPA-E sourced diagram of a Harvard flow battery is sufficient to start the discussion. The “flow” in flow batteries is for the movement of liquids through two chambers separated by a polymer membrane that allows the passage of subatomic particles between the chemicals.

Harvard redox flow battery diagram courtesy of ARPA-E
There are often four tanks, not two, so this diagram represents one of the models. The pumps push liquids from a tank or two through the chambers into the other tank or two. As they pass through the chambers over the membrane in the presence of electricity, charged particles move from one chamber to the other through the membrane and the liquids’ chemical composition changes. What ends up in the storage tank(s) are different chemicals than what was being pushed through, and the new chemicals have stored a charge.
Reversing the pumps pushes the new chemicals back through the chambers and the charged particles migrate back through the membrane, reversing the chemical process and releasing electricity. In closed-loop flow batteries, you end up with exactly the same chemicals you started with and can repeat the process as many times as you like. Open-loop flow batteries raise very interesting possibilities, and more on that later.
For a sense of scale, a MWh of storage requires typically tons of liquid, but MWh storage in lithium-ion batteries weigh a lot too. An 85 KWh Tesla Model S battery weighs 540 kg or 1,200 lbs, so a MWh version would weigh around six tons. Also contextually, pumped hydro sees examples such as a gigaliter of water for a GWh of storage, suggesting tens of thousands of tons of water for a MWh. Energy storage requires mass.
A flow battery will look like a shipping container or small building surrounded by two to four large tanks, pumping equipment, and electrical grid connection and electricity-management components. It will look more like a chemical plant, not a battery, and there’s a thread there that I will pull on in a subsequent article.
The chambers and membranes have limitations in terms of scale. This isn’t one chamber and one membrane, but many chambers and membranes. It’s not one set of tubes leading to a single chamber, it’s a lot of sets of tubes leading to a lot of chambers.
Once again, the analogy can be made to Tesla’s battery packs. They use a lot of small battery cells connected in series to achieve the voltage required and then in parallel to create the capacity required. The difference is that the contents of the lithium-ion battery remain in place until they degrade and battery capacity is lost and the individual cells have to be replaced entirely, but the flow batteries use chemicals which are easy to replenish as necessary.
Scale is also important. While Tesla’s individual battery cells have increased in size, they are still the size of a finger. You can hold a lot of them in one hand. They look like bigger versions of the AA batteries we put into our handheld electrical devices like razors and flashlights. There are about 4,400 of them in a single Tesla Model 3 to achieve the kWh of storage that a car requires to drive hundreds of kilometers.
Flow battery cells, on the other hand, are much bigger as individual components. Agora’s founders tell me that their individual cells will be scaled to 0.5 meters by 0.5 meters square and 1.0 centimeters thick on the inside, and a bit more than that with structural components and hose and electrical fittings. That’s 1.6 ft by 1.6 ft and perhaps half an inch internally, and perhaps 2-4 inches thick with the remainder. Their cells will have a capacity of processing various flow rates of liquid electrolyte, and room for the gaseous CO2 as well, a unique aspect of their technology.
The scale is part of what makes flow batteries interesting. Let’s take a brief digression into vertical vs horizontal scaling, or scaling up vs scaling by numbers, as my chemical plant engineer collaborator Paul Martin says they refer to it in that industry.
Vertical scaling makes individual components of a system bigger and more powerful. In computing, it leads to mainframes. In energy, it leads to GW nameplate capacity nuclear and coal plants. But vertical scaling above a certain point turns into a lot of engineering at the point of construction. Things get to a scale where they can’t be shipped, so they are delivered broken down into an often complicated 3D jigsaw puzzle of components that have to go together in a certain order with skilled resources assembling them. The history of failures of nuclear plants to be delivered on time and budget is testimony to the challenges of vertical scaling. In other words, scaling something up is good until it isn’t good any more.
Horizontal scaling, on the other hand, uses a lot of small, identical components to create the same output as a single vertically scaled component. In computing, that’s distributed server technology. In energy, that’s wind and solar farms. With horizontal scaling comes manufacturability of the individual identical components including factory quality control. And it provides for very standardized distribution and highly parallelized modular construction at the sites.
This variance between the massively vertically scaled central power stations vs the massively horizontally scaled wind and solar farms is a very poorly understood competitive differentiator in the energy industry. It’s part of the reason, in my opinion, why energy analysts failed miserably to understand how much wind and solar were going to eat coal and nuclear plants. The analysts in that industry had no context for horizontal scaling and the enormous economies of that type of scaling. After all, there are only about 500 working nuclear plants in the world. A GW of wind energy capacity might have 400 wind turbines, and given capacity factors a wind farm that’s equivalent to a single nuclear plant might have 800 wind turbines. That’s an awful lot more identical manufactured components with identical templated assembly and a lot of room for optimization at every step of the supply and construction chain.
Solar panels, of course, are even more horizontally scaled than wind turbines, with 200 kW panels a meter long weighing 30 kg or so, but tens of thousands of them. Solar panels are like chopsticks, manufacturable in massive volumes easily and cheaply, easy to stack in containers, easy to ship around the world, and easy for teams of humans to put on racks.
Horizontal scaling comes with its own challenges. If the components are too small, say the size of a human finger, it takes a lot of connections to achieve a very large output. That doesn’t make them ineffective or inefficient as the Tesla example shows very clearly, but it does suggest that there are advantages to scaling in both directions. The plummeting cost of solar shows that meso-scale objects that are manipulable by individual humans, that come in very regular dimensions and that have simple assembly processes on site have a lot of advantages.
Which is where we return to flow batteries. That 0.5m x 0.5m x 1 cm cell is about the size of a blade server in computing. Without liquid, it will weigh perhaps 0.5 to 0.8 kg approximately since most of it is carbon-based material, polymer membrane, and plastic. In other words, it’s in the scale of the devices that run the internet already and it’s in the scale where it’s easy for humans to manufacture, distribute and assemble in large volumes.

Diagram of redox flow storage system courtesy Sandia Labs
This image from a Sandia Labs presentation on energy storage starts to cement this. If I had said this was a server rack set and associated equipment, you would have believed me. But this is the type of thing you will see with flow batteries. The cells will slot into standard racks. They will have standard connections. Semi-skilled labor will be able to connect them together following Ikea-class instructions. There will be a lot fewer connections for a given scale of storage than using Tesla’s finger-sized batteries.
And the other aspect of flow batteries, that they have externalized chemical loads instead of the embodied chemistry of lithium-ion cells, has advantages as well. They are much lighter per unit when shipped, and completely inert. The chemicals will be stored in bog-standard industrial tanks, commoditized components that are easily shipped and assembled as well. Shipping tanks of chemicals is a very commoditized market as well.
This is not to say by any stretch that Tesla’s Powerpack is inferior, it just has different characteristics that mean its economics for manufacturing and distribution are different. The individual batteries are manufactured in highly automated factories and are very amenable to automated packing and distribution. Getting them all wired together into battery packs for cars or grid storage is also automatable. And they don’t need plumbing at point of installation, which is an advantage, just wiring. They also have a great deal more flexibility of use. I’ve seen proposals for flow batteries in cars, which is even less intelligent than putting hydrogen fuel cells in cars, although not as bad as Saudi Aramco’s tailpipe carbon capture nonsense.
One of my relevant recent experiences was working on a 6-year technology strategy for a global electronics manufacturer. (Neat trivia: they built a factory in Laos for the cheap land and labor, but strung their own internet cable across a bridge from Vietnam to gain stable connectivity of sufficient bandwidth.) Among other things, they build fully loaded racks of blade servers and components, built and tested in one of their Asian factories for major brands like HP and IBM. This suggests that flow batteries will be delivered to sites the same way fairly rapidly. They will be assembled into individual racks in factories, have strong quality control as manufactured objects, then be wrapped and shipped in standard shipping containers to sites where the racks will be mounted and the connections made. It’s likely that all of the plumbing and wiring for each rack will converge into one electrical input and output and two to four plumbing inputs and outputs. Depending on optimization, racks could contain dozens of pre-wired and pre-plumbed cells, ready to be placed in rows in a lightly air conditioned building.
And there’s a further thought down this optimization path. One of the things that Google does with its data centers is to turn them into container farms. They take standard shipping containers, outfit them with racks, stick blade servers in the racks, put in all of the air conditioning, power and connectivity components, then ship them using standard container transshipment distribution to leveled fields where there’s cheap electricity near dams. They drop an entire container, hook it up from the outside to power and the internet, and walk away. When the container’s servers degrade to a sufficient level, they pick up the entire container and ship it back to the factory for replacement and refurbishment. That’s likely the end point of flow battery optimization as well.
Flow batteries have useful operational characteristics as well. Because they don’t have the chemicals embodied in the cell and because the chemistry is sufficiently different, they don’t have recharging limitations. Tens of thousands of cycles are trivial for flow batteries, which is an advantage for grid storage.
That doesn’t mean that they last forever or that they don’t have other constraints. Common chemistries such as vanadium redox flow batteries use toxic and acidic chemicals, so the transportation and siting comes with health and safety constraints. The corrosiveness needs to be engineered for. The membranes and catalysts degrade over time as well, and need to be replaced.
But maintenance can be easy as well. Because of the serial and parallel nature of a flow battery, you can shut down a string of racks and only reduce the overall capacity, not disable the storage in total. Because of the human scale of the cells, you can foresee a maintenance person pulling a cell out of a rack, putting a new cell in and shipping the cell off for refurbishment. And of course the end model of shipping containers going back to the factory is viable as well.
Flow battery characteristics typically mean that they are most cost effective at grid or major facility scales of storage. Per my assessment, most are useful for mid-duration storage of 6 to 48 hours. This means that they overlap nicely with the load shifting of more expensive Tesla-approach lithium-ion storage for in-day, fast response grid balancing and with 1-21 day storage in GWh-scale pumped hydro. I see each of the storage technologies have a place to play on well balanced grids.
This is part of a series of articles I’ll be publishing around this technology. At least two will be devoted to Agora Energy, as they have a unique chemistry and model based on a couple of fundamental insights which gives them what appears to me to be a very strong advantage in two different domains.
Full disclosure. I have a professional relationship with Agora as a strategic advisor and Board observer. I did an initial strategy session with Agora about their redox flow battery technology in late 2019 and was blown away by what they had in hand, and my formal role with the firm started at the beginning of 2021. I commit to being as objective and honest as always, but be aware of my affiliation.

You may like
Environment
Hyundai commits a record +$16.6 billion in Korea to develop new tech and EVs
Published
1 hour agoon
January 9, 2025By
admin
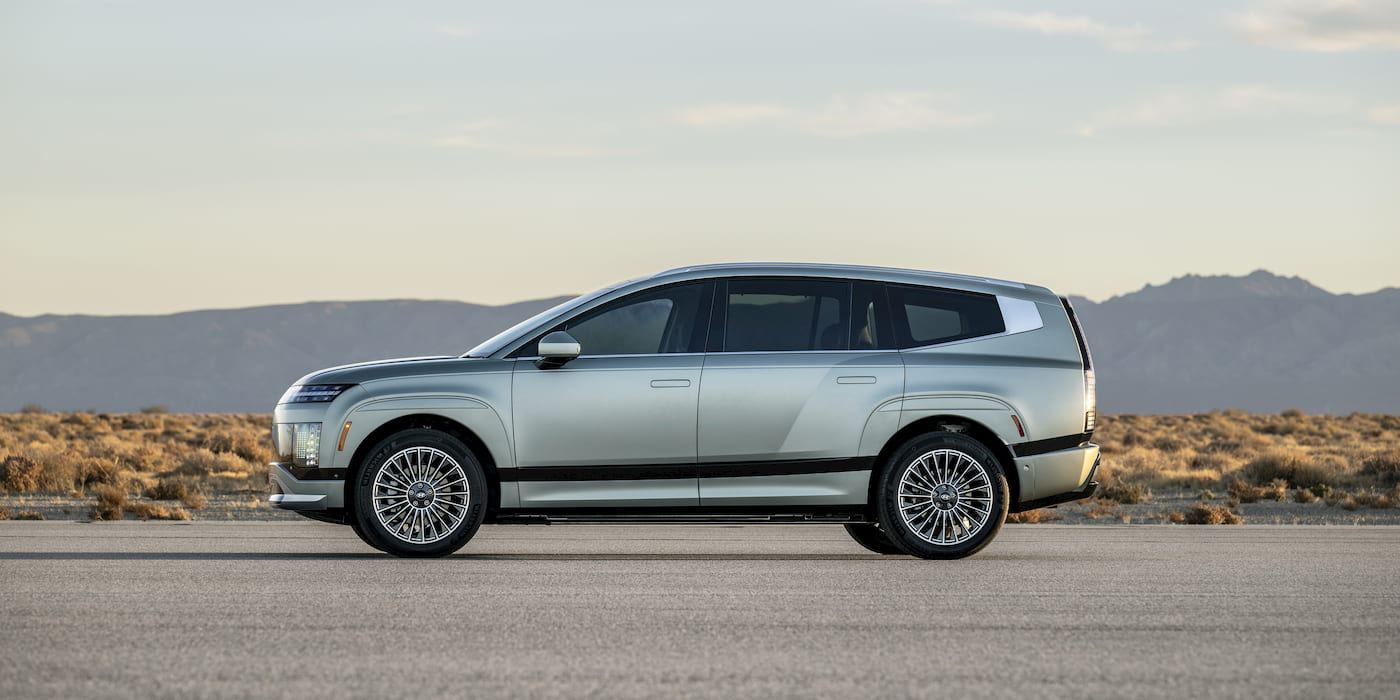
The world’s third-largest auto group is going all-in to lead the shift to electrification. With plans to pour a record over $16.6 billion into advancing new tech and EVs in South Korea, Hyundai is laying the groundwork for the future. Can the new investment help it surpass Volkswagen or Toyota in global sales?
Hyundai Motor Group, including Kia, announced on Thursday that it will “make the largest annual investment in its history in Korea this year.”
In 2025, Hyundai plans to invest KRW 24.3 trillion, or over $16.6 billion, in its home market. This is up 19% from the previous record of KRW 20.4 trillion (about $14 billion) set in 2024.
Hyundai said the reason behind the record investment “is because it believes that continuous and stable investment is essential to overcome the crisis and secure future growth engines.” A big part of the crisis Hyundai is referring to started last month.
After President Yoon Suk Yeol declared martial law and was later impeached on December 14, South Korea plunged into a political crisis. Korean buyers are hesitant to make big purchases, which has slowed demand.
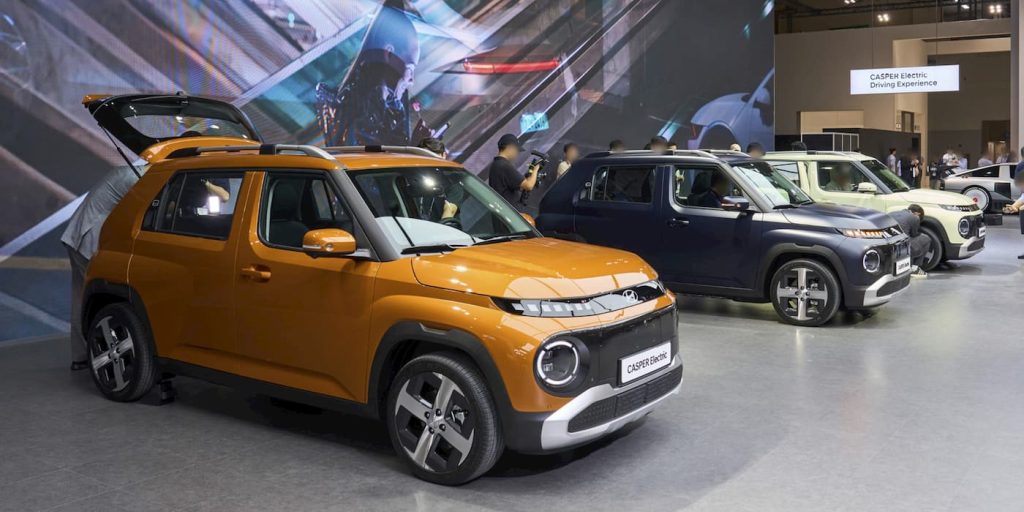
Hyundai’s global sales slipped nearly 2% in 2024. Although sales outside of Korea were roughly flat, domestic sales were down 7.5%.
To boost growth in 2025, the auto giant is pouring resources to accelerate the development of new tech, EVs, and software.

Hyundai is doubling down on new EVs and tech
Hyundai said its focus this year is “on new business areas such as development of next-generation products, securing key new technologies, and accelerating electrification and SDV.”
The company will invest KRW 11.5 trillion ($7.9 billion) into R&D “to secure key future capabilities such as improving product competitiveness, electrification, SDV, hydrogen products, and development of original technologies.”
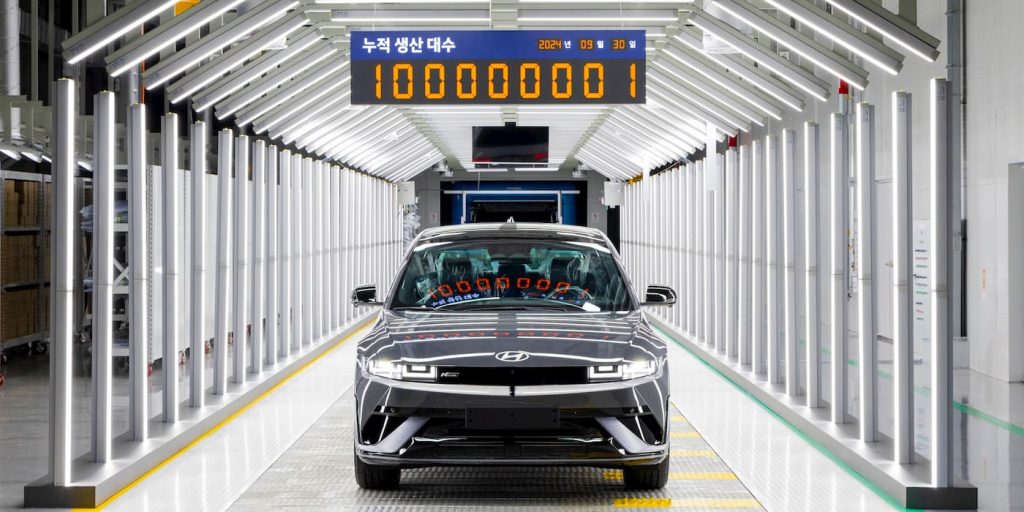
Another KRW 12 trillion ($8.2 billion) will be used to ramp up domestic EV production and improve manufacturing. Hyundai plans to continue making large-scale investments to build EV-only facilities in 2025.
Last year, Kia began production at its new Gwangmyeong EVO Plant, where it builds the new EV3. Later this year, Kia will start mass production of its PBV electric vans.
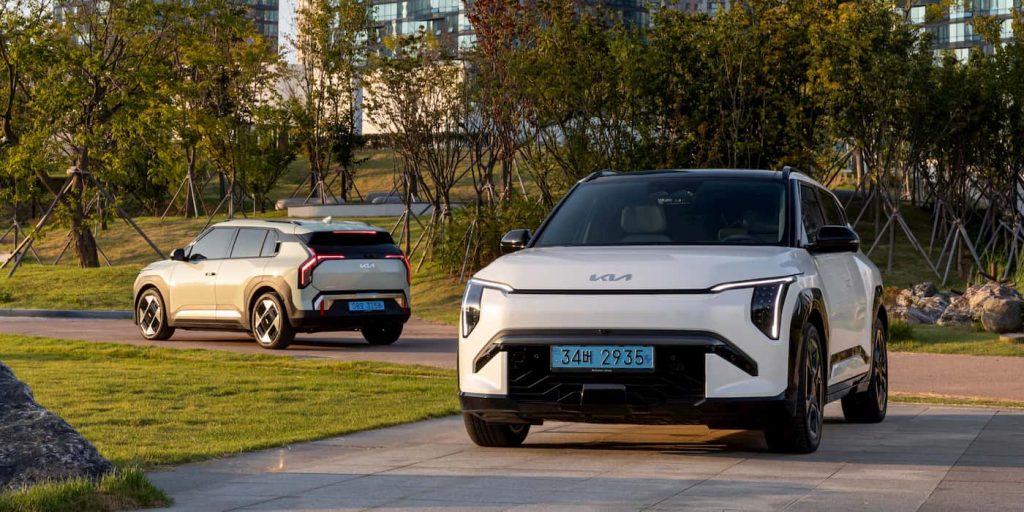
Hyundai will open its dedicated EV plant in Ulsan in the first half of 2026. The company plans to mass produce EVs, starting with an ultra-large electric SUV.
In the US, its most important market, Hyundai just opened its new $7.6 billion EV plant in Georgia. The first vehicle to roll off the assembly line was the upgraded 2025 Hyundai IONIQ 5, which now has more range, better style, and a NACS port for charging at Tesla Superchargers.
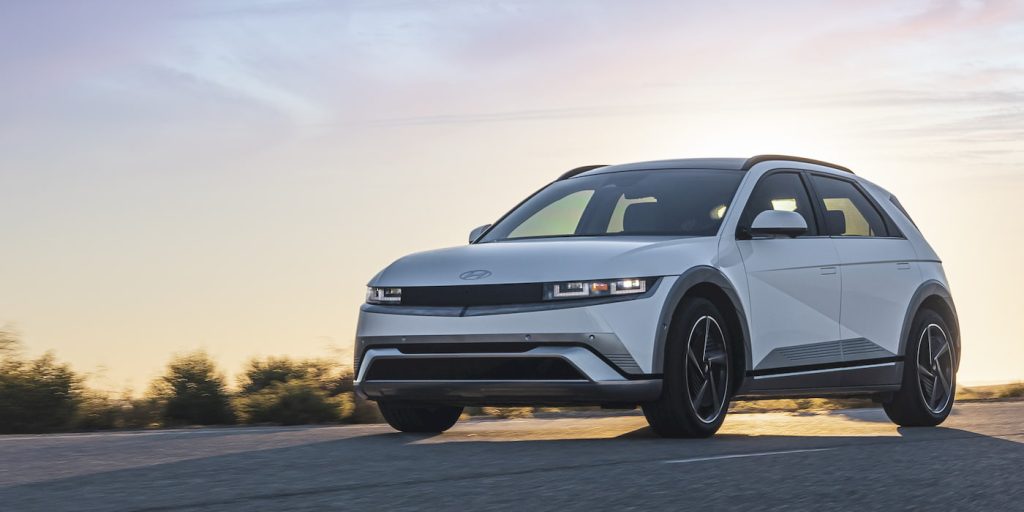
Hyundai will begin building its first three-row electric SUV, the IONIQ 9, in Georgia in Q1 2025. The larger electric SUV will be available in the US and Korea in the first half of 2025.
With several Hyundai Motor, including Kia and Genesis, EVs now eligible for the $7,500 federal tax credit, can Hyundai gain an advantage over the competition?
Hyundai is also the first company to sell its vehicles on Amazon in the US. The new 2025 IONIQ 5, IONIQ 6, and Kona Electric can now be purchased directly on Amazon’s website.
FTC: We use income earning auto affiliate links. More.
Environment
Los Angeles is awful to get around. But this scooter made it work!
Published
2 hours agoon
January 9, 2025By
admin
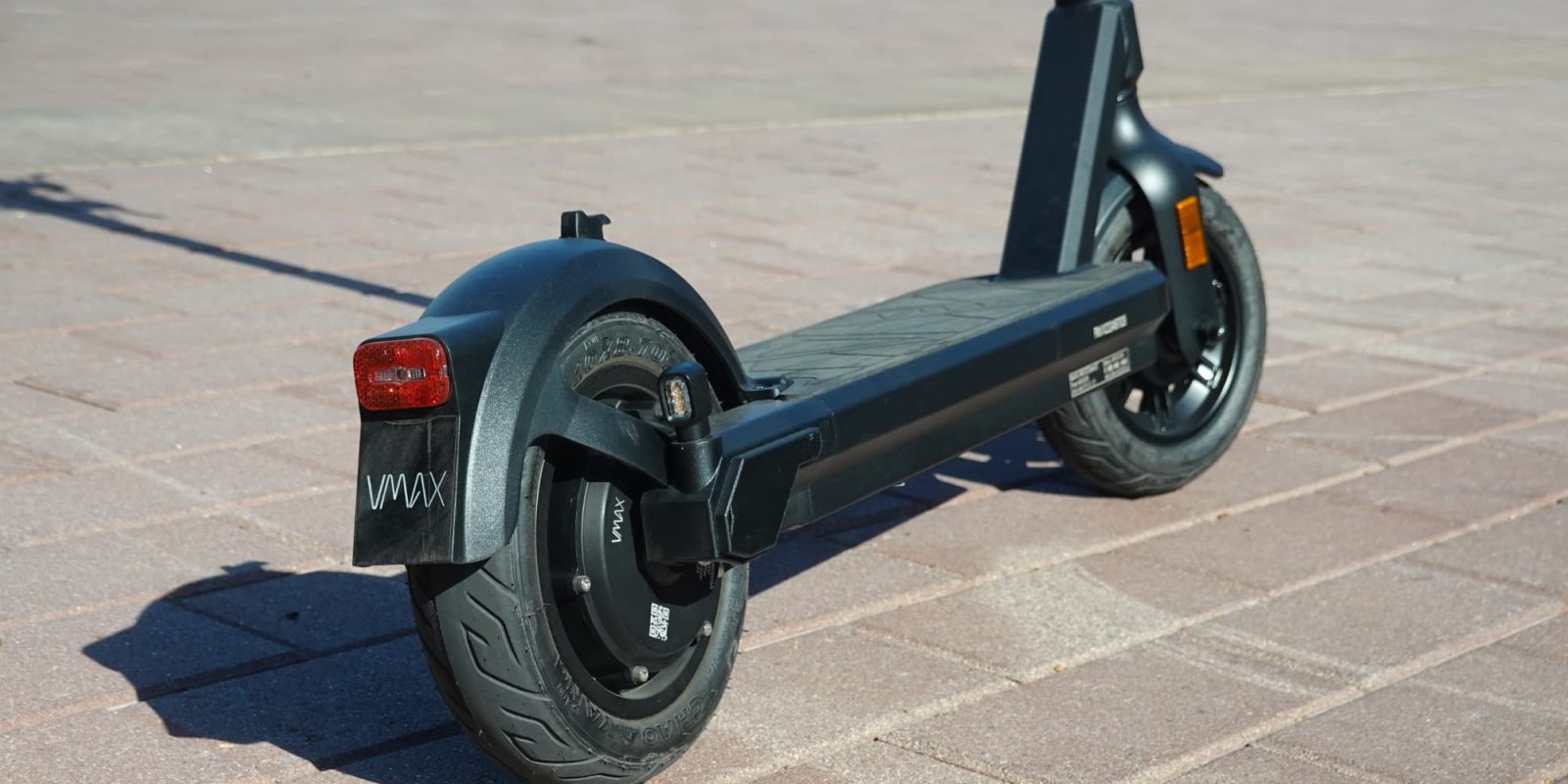
Last month, I had the chance to visit Los Angeles and attend Micromobility America, a yearly industry tradeshow focusing on e-bikes, e-scooters, and other small-format vehicles. To get around the city for a few days, I borrowed a VMAX VX2 Extreme from VMAX’s Los Angeles distribution center and it made all the difference in navigating a city that is notoriously hard to get around.
My regular readers and viewers will know I’m an e-bike first guy, but that I won’t say “no” to any form of micromobility. I’ve ridden almost everything, so you can bet that I count electric scooters in my stable, too, even if it’s predominantly comprised of e-bikes. And I must say that there’s something nice about being able to stash your scooter in the trunk of an Uber or under a train seat when necessary.
While in LA, I was excited to finally get a chance to review a VMAX scooter, since I’ve followed the company’s US expansion with interest over the last year or so. As a Swiss-based company, VMAX first found success in Europe before expanding into the US with larger and more powerful models.
The company let me borrow a VX2 Extreme electric scooter, which is a 25 mph (40 km/h) scooter that is surprisingly powerful. It doesn’t look much bigger than a dirt-cheap GoTrax or similar budget scooter, yet it is much faster and more powerful—to the tune of 1,600W of peak power.
You can see how it rides in my video review below, or keep reading for the whole story.
VMAX VX2 Extreme Video Review
Becoming a scooter guy in LA
LA is notorious for being difficult to navigate, and even if you have a car, that doesn’t mean you’ll be getting anywhere quickly. Depending on who you ask, the public transportation system is either a trainwreck or somewhat decent, though no one will tell you LA has well-developed public transit.
That’s why I knew I wanted to be able to rely as much as possible on my own independent transportation while in the city, and a scooter made sense. With the VMAX’s 25 mph top speed, I could keep up with most city traffic, yet I could still easily stow it to fit in the trunk of a rideshare car or stash it in my hotel room without drawing much notice from the front desk.
My trip started with visiting VMAX’s distribution center in downtown LA, which had me taking a 30-minute walk that was both refreshing and a great reminder of how slow it is to get around a massive metropolitan area on foot alone. Don’t get me wrong – I love walking and I also use jogging as my primary form of exercise. But a pair of shoes just isn’t a very fast or efficient transportation method in a big city.
After getting to tour VMAX’s large warehouse and see how they fulfill customer orders from all over the US (as well as get a look at several different models they offer), the team let me borrow a VX2 Extreme and sent me on my way. My next stop was an event down in Costa Mesa near Irvine, which Google Maps told me would be a 43-mile (69 km) journey from Downtown LA, and which just so happened to be the exact range of the longest range version of the VX2 Extreme scooter (it comes with three battery options of between 28-43 miles of range depending which battery size you choose).
However, those range ratings are rarely at the scooter’s maximum speed and power level, which I intended to be rocking for most of the trip. But Google Maps suggested to me that it would be an easy train ride instead, with just a couple miles of scooting to and from the train station on either end. Awesome!
I scooted on over to the train station and arrived just in time… to miss the train by two minutes. No worries, back home there’s a train every 10 minutes or so. I checked the train schedule and to my horror, the next train wasn’t scheduled for more than two hours from now. Thanks, LA.
I didn’t have that kind of time – I’ve got a micromobility conference to get to! So I had to swallow my pride and order an Uber. Fortunately the scooter folded up and fit easily in the trunk along with my travel backpack and my camera backpack. That’s not something I can normally do on my e-bikes!
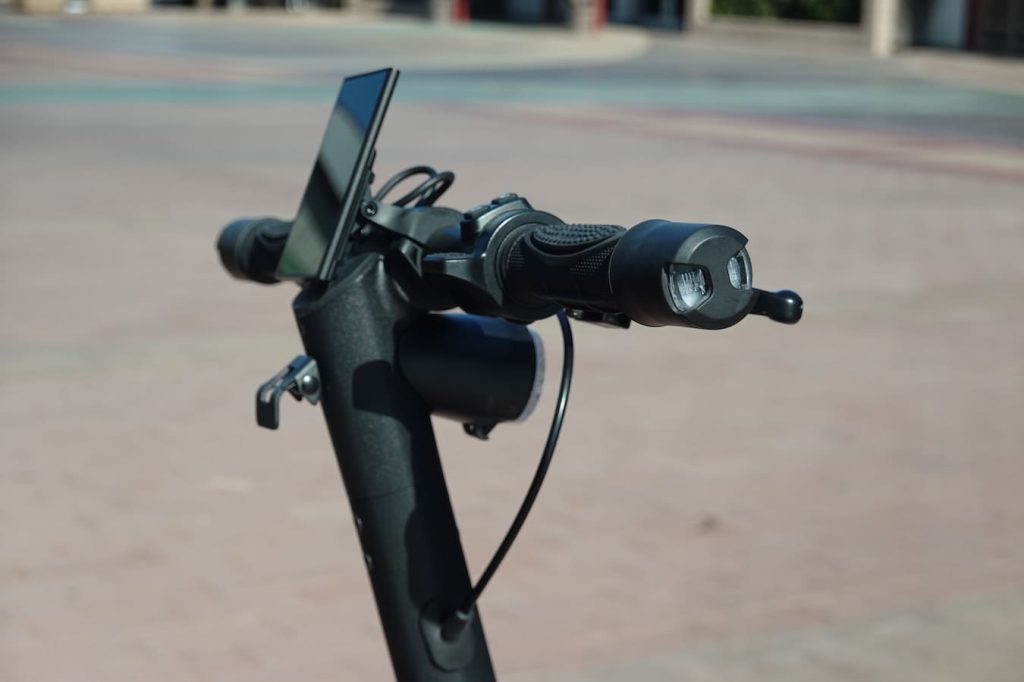
Forty-something miles later, I was in Costa Mesa with time to spare, which I spent happily burned by scooting around. It was my first chance to spend more than a couple of rushed minutes riding the scooter more pleasurably to get a real feel for it. The VX2 Extreme doesn’t have suspension but still felt quite good on the city streets, even when hopping the occasional curb or speed bump.
The build is obviously quite robust, without giving me the rickety feeling I get on cheaper quality scooters. And the power is surprisingly potent. When I put the scooter in its highest power setting, known as Beast Mode, I would often accidentally wheelie it while starting, since I tend to keep my rear foot on the board and push off with my front foot. Those wheelies were fun, but I decided to mostly scoot around in one notch below the highest power mode, as that felt more reasonable for everyday riding. But it’s nice to know you’ve got more power than you need, instead of merely maxing it out 100% of the time.
As the winter sun set quickly, it gave me my first chance to check out the lighting and turn signals on the scooter. Those turn signals are actually quite bright during the day, lighting up the handlebar ends up high for better visibility, as well as motorcycle-style turn signals down low on the rear of the scooter. The rear turn signals are flexibly mounted, meaning they can bend and bounce back into position instead of breaking when they inevitably hit something.
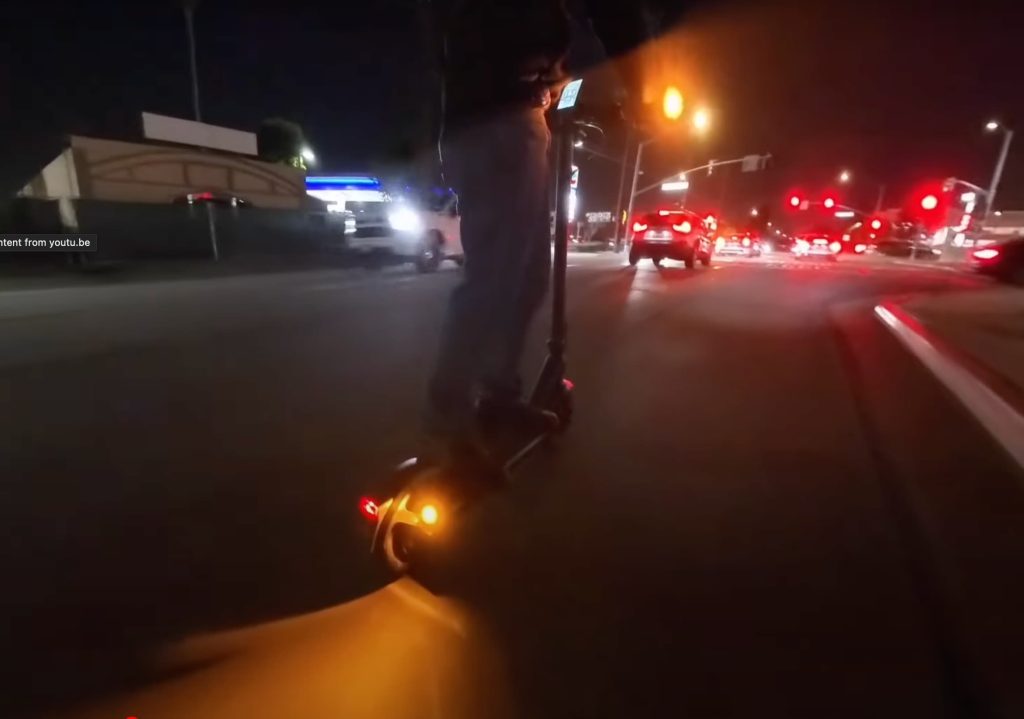
The turn signals were weirdly impressive. You can see in the image above how the lower ones light up the road and the upper ones are quite visible by sticking out to the sides on the handlebar ends.
Normally, I deride most e-bike and e-scooter turn signals because they’re typically diminutive and unclear, mostly serving as a flashing light so close to the vehicle’s centerline that they don’t achieve their goal of actually indicating direction. But VMAX has done a great job with these, as they’re both attention-grabbing and clearly indicate that you’re about to turn—which is important when quickly riding around cars at night.
I also found the speed of the scooter to be both a blessing and a curse. I forgot that LA weather isn’t always “Santa Monica in June”, and I was absolutely freezing in my hoodie – the only garment with long sleeves that I had packed.
Flying fast at 25 mph down wide Costa Mesa roads wasn’t helping, with that airstream cooling me even further. I had to decide between going faster to get to dinner sooner at the risk of turning into an icicle along the way or slowing down to cut the windchill. Unfortunately, the battery was so large that I couldn’t use the efficiency argument to encourage me to slow down, so I just continued bombing it down to the Balboa Peninsula at 25 mph, meeting up with friends to offer freezing cold handshakes and high-fives. Dinner was great, but the ride back was even colder. I thought I might go slower climbing the hills on the way back from the coast, but the dang thing zipped up the hills fast enough to keep my fingers feeling like they were encased in ice. But hey, at least the fast speed meant I could shorten the trip as much as possible!
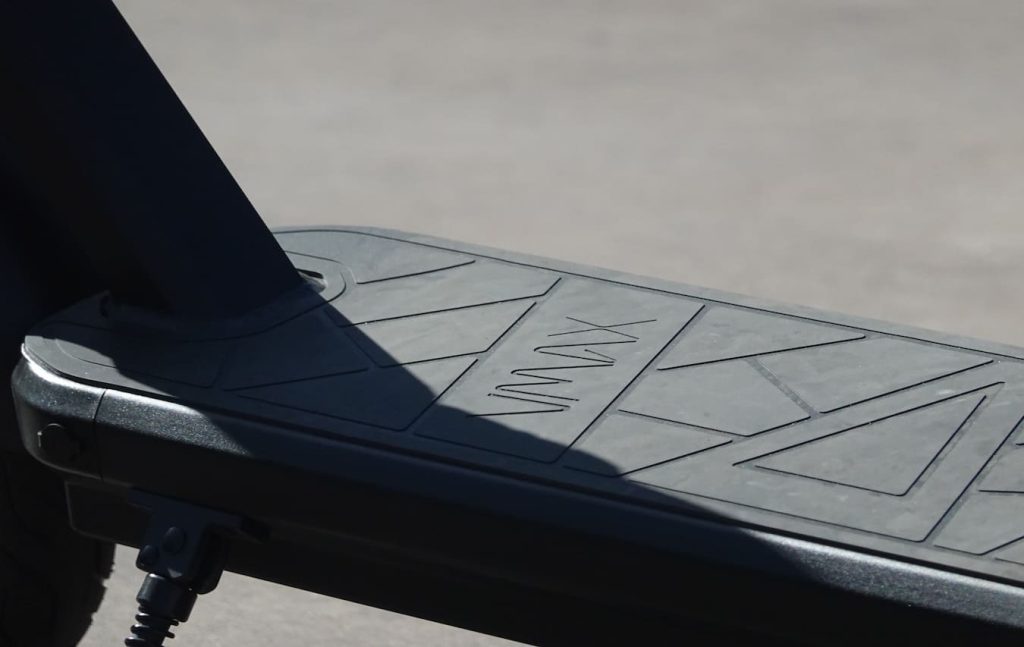
The next day, I scooted to the show in the morning and found that the fairgrounds where it was hosted were closed off at most entrances. I guess they do this to limit how cars can enter (and ensure everyone gets charged to park), but I was an elitist with my own right-sized transportation and not about to let things like traffic control stop me!
Some scooting across the weeds and carrying the 45 lb (21 kg) scooter over a couple barricades later, I was in! I’m not saying you should ride in places you aren’t allowed, but just that there’s an advantage to being able to take creative routes when the vehicle you drive weighs as much as your leg.
I locked up at a bike rack and made it to the show in record time, taking full advantage of the fact that micromobility vehicles often allow you to chart your own path.
That was how I got around for next two days, putting around 30 miles (50 km) on the scooter. I charged it each night at my hotel, but I never used more than 30% of the battery, so I’m not sure I really needed to charge it all.
Ultimately, the VMAX VX2 Extreme scooter proved to be an ideal way to navigate the city. I took it on many rides, both for my morning and evening commute, as well as to meet up with friends and simply scooting around for pleasure. It always offered me more than I needed, both in terms of power and range, and felt comfortable while doing it. The 10″ tubeless pneumatic tires have enough squish to give me some comfort on rougher patches and are large enough diameter to handle all the sidewalk cracks and minor potholes I threw at them.
Basically, I was pretty darn happy with it. Of course you pay more for such a well-built scooter from a Swiss company, to the tune of $899, but it seems quite fair to me. It’s a long range and incredibly powerful scooter that hides in a surprisingly portable package, easy enough for me to toss in a vehicle or carry over a chain barricade. And with the extra features like safety lighting with turn signals, the 1,600W of peak power, the easily readable 4″ color TFT screen, the weather-sealed drum brakes combined with electric motor braking, and the stable folding design, the scooter treated me better than well for my three days riding it around central and southern LA.
VMAX has other even more affordable models starting from around $400, but I’d say the VX2 Extreme is a great Goldilocks option that offers more power and range than most people need in a portable package at a fair price.
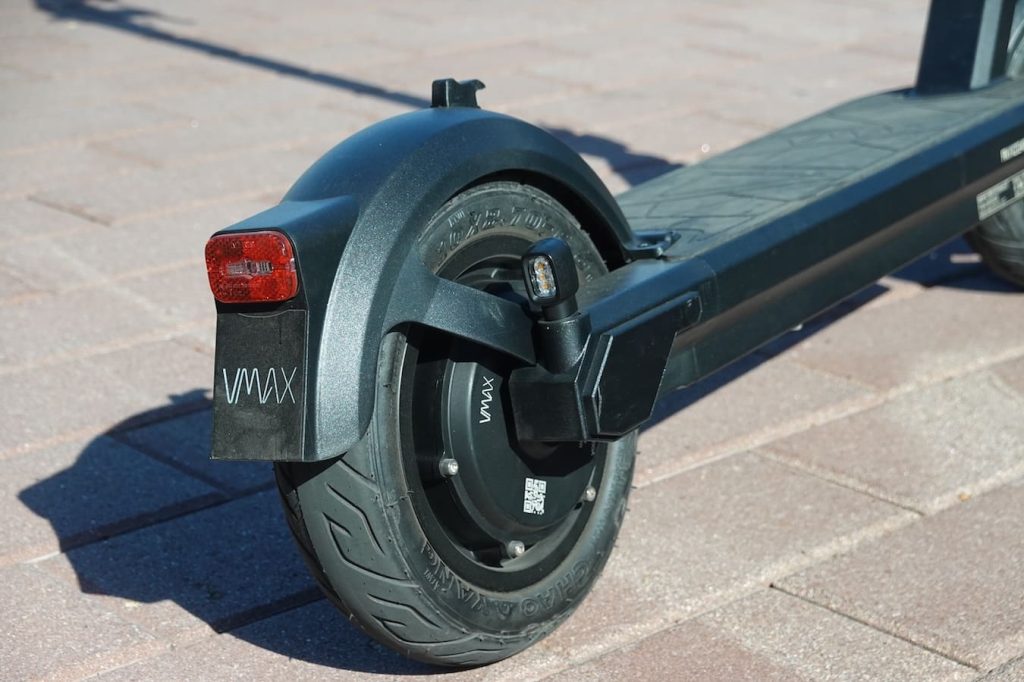
FTC: We use income earning auto affiliate links. More.
Environment
Can Model Y refresh reignite Tesla’s growth?
Published
2 hours agoon
January 9, 2025By
admin
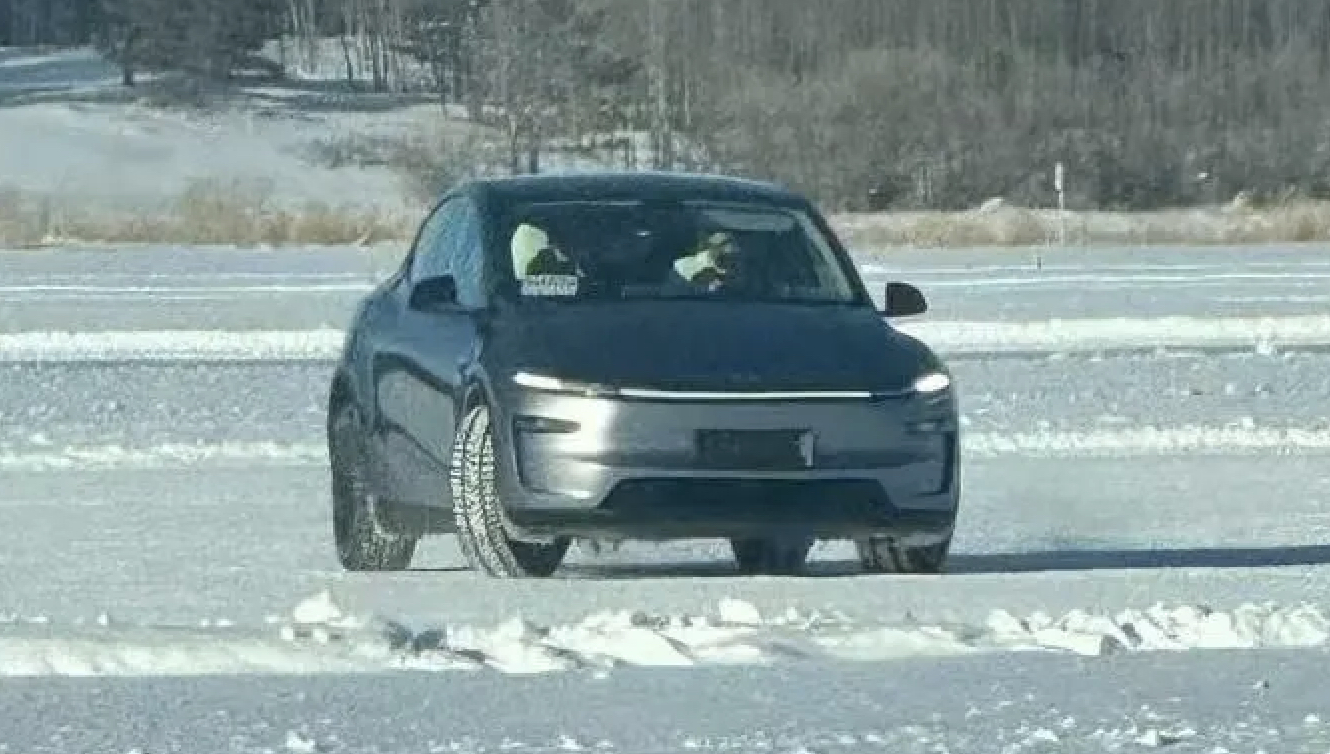
Tesla is about to release a design refresh for Model Y, its most popular model, and it raises an important question: can it reignite Tesla’s growth?
Fortunately, we have a good recent comparison since Tesla refreshed the Model 3 last year.
Tesla doesn’t break down sales per model so we have to rely on third-party data to track Model 3 sales.
There are varying estimates, but most of them are putting Tesla Model 3 sales between 500,000 and 530,000 units in 2023 prior to the refresh.
In 2024, estimates are putting sales at roughly the same.
Tesla delivery analyst TroyTeslike has data pointing to 520,000 Model 3 deliveries in 2024. The production changeover has certainly affected sales in the first of the year, but it looks like production and deliveries peaked in Q3 as Troy has Model 3 at the same volume of about 149,000 units in Q3 and Q4.
As with all other Tesla models, the peaked delivery volumes were also achieved with record incentives and discounts in Q4.
Can Model Y refresh be different?
Model 3 refresh didn’t help the program that much. It is virtually doing the same delivery volumes it was last year, but it doesn’t necessarily mean the same will happen with Model Y.
A lot of that depends on the refresh itself.
Earlier today, we had our best look at the refresh so far, and it is similar to the Model 3 refresh in the sense that it features new headlights and taillights, although different ones than Model 3, including light bars, as well as a more aggressive front-end.

The level of exterior changes is similar to the Model 3 refresh in terms that it is significant but not massively different either.
Tesla didn’t go into too many details about “under the hood” changes with the Model 3 refresh, but it did feature an improved suspension, a quieter cabin, and a slight increase in efficiency.
We can expect similar improvements to the Model Y.
There were some changes that people saw as negative, with the main one being the new steering wheel. Model Y is still the only vehicle in Tesla’s lineup that doesn’t have a stalkless steering wheel with force touch turn signals and a gear selector on the center display.
Considering all other Tesla vehicles went that way, this is expected to change with the Model Y refresh. Personally, I didn’t have any problem adapting to the new turn signals when driving the new Model 3 and Cybertruck, but I do admit that the gear selector is annoying.
I know many Tesla fans refused to get a Tesla vehicle with steering wheel stalks.
Electrek’s Take
Based on the information we have right now, I would expect the Model Y refresh to have a similar impact as the Model 3 refresh, but we could get a surprise.
Obviously, if there were significant improvements to the range, that would make a big difference, but I would only expect small incremental improvements at best.
A bigger surprise would be Tesla bringing something like the steer-by-wire and a 48-volt architecture from Cybertruck to Model Y. You have to try it to appreciate it, but the steer-by-wire on Cybertruck is super fun.
The design update looks good, but I thought the Model 3 redesign was even sharper, and it didn’t have much of an impact. I think new features or more efficiency/range would be the most significant difference makers.
What do you think? Let us know in the comment section below.
FTC: We use income earning auto affiliate links. More.
Trending
-
Sports2 years ago
‘Storybook stuff’: Inside the night Bryce Harper sent the Phillies to the World Series
-
Sports9 months ago
Story injured on diving stop, exits Red Sox game
-
Sports1 year ago
Game 1 of WS least-watched in recorded history
-
Sports2 years ago
MLB Rank 2023: Ranking baseball’s top 100 players
-
Sports3 years ago
Team Europe easily wins 4th straight Laver Cup
-
Environment2 years ago
Japan and South Korea have a lot at stake in a free and open South China Sea
-
Environment2 years ago
Game-changing Lectric XPedition launched as affordable electric cargo bike
-
Business2 years ago
Bank of England’s extraordinary response to government policy is almost unthinkable | Ed Conway